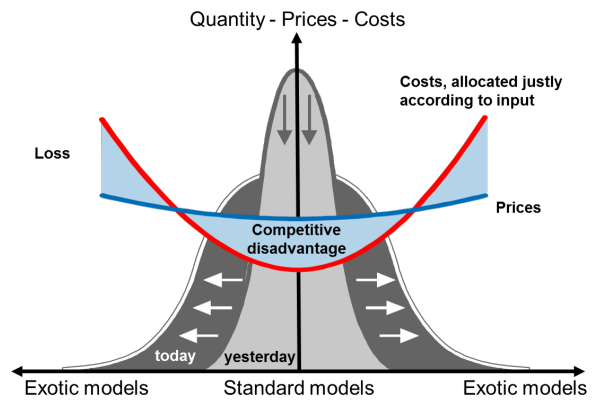
Chart: RWTH Aachen University
Researchers have worked intensively for one-and-a-half years across national borders to find ways of reducing the costs of solar thermal systems and making them more attractive to end users. The members of Task 54 of the IEA Solar Heating and Cooling Programme, Price Reduction of Solar Thermal Systems, have discussed the effects of standardised product designs or changes in product offerings on cost structures. They have also analysed the entire value chain from component manufacture to system assembly and installation to help identify cost-cutting potential. This is the first time that methods of Process Cost Analysis are being adapted for the solar thermal business. “The share of overhead (e.g. marketing, sales, logistics, quality management and maintenance) has increased significantly, from 30 to 60 % of total product expenses over the last 50 years. This means we will have to investigate the relationship between technology, product portfolio and overhead,” explained Wolfgang Kramer, Head of the Solar Thermal Heating Systems Department at German-based Fraunhofer ISE. “To this end, the process cost analysis provides important quantitative information.” For example, the chart illustrates the issue of having a wider product portfolio and its impact on competitiveness and profitability. The model is currently being adapted for the solar industry in Task 54 as part of German research programme TEWIsol.
The German research partners from Fraunhofer ISE are using the newly adapted methods to optimise the cost structure of the value chain in cooperation with German-based RWTH Aachen University. “We have expanded upon the methods used by Aachen University to create ones which meet the needs of the solar industry, which means adding the plumber business and factoring in the solar thermal yield,” said Kramer. The research has been funded by the German Federal Ministry for Economic Affairs and Energy as part of the TEWIsol project (which aims to improve the technology and cost efficiency of solar combi systems).
“Process cost analysis leads to a change of business culture in manufacturing, as expenses incurred due to an adaptation of a standardised product are quantified to make management see the losses made with an exotic one, which the company sells only in small numbers,” explained Frederic Diels, researcher at RWTH Aachen’s Laboratory for Machine Tools and Production Engineering and partner within TEWIsol. In general, manufacturing businesses allocate costs not directly related to production in equal shares to all their products (as illustrated by the blue line in the chart above), which makes standardised “cash-cow” items relatively expensive and favours exotic units produced in small series. The “just allocation of costs based on input” is shown by the red line in the chart above, which places a higher cost burden on exotic products.
Process cost analysis quantifies expenses in the supply chain incurred when offering special-purpose units (exotic models). These also include overhead, for example, costs to certify material suppliers, establish product registration numbers, create product flyers and train service staff, etc. “By adding up all these indirect expenses across the value chain, management becomes aware that they might lose money with product variants if they do not sell a lot of them,” explained Diels. Kramer said that it was the first time that the methods were being used for the entire value chain of the solar thermal industry and related services (plumbers) and that they could help optimise cost structures.
The TEWIsol research partners have been implementing the new methods at two German industry partners, manufacturer Meibes System-Technik and installer SWB Sonnen- und Windenergieanlagenbau to verify their effectiveness. TEWIsol’s progress is reported in the framework of IEA SHC Task 54. The results will be presented at a workshop in late 2018.
Websites of organisations and projects mentioned in this news article: